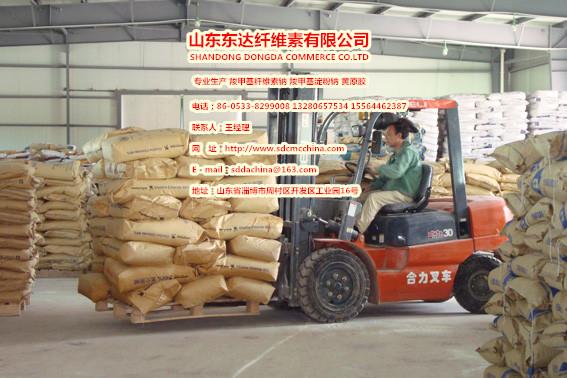
淀粉微球因具有特殊的載藥靶性和較好的吸附性而受到廣泛重視•形成穩(wěn)定的乳液是制備微球的 基礎(chǔ),由于乳液的形成是一個(gè)介觀過程,因此研究其微觀結(jié)構(gòu)變化及其對(duì)性能的影響難度較大.通過 計(jì)算機(jī)模擬建立在原子水平上的分子動(dòng)力學(xué)方法對(duì)于一些簡(jiǎn)申的體系十分有效,但對(duì)相對(duì)復(fù)雜體系的 計(jì)算則相當(dāng)困難
由HoogerbmggeP% Koelman等[3]提出的耗散粒子動(dòng)力學(xué)(DPD)方法常用來模擬流體的動(dòng)力學(xué)行 為,如表面活性劑在油/水界面的分布狀況等[4_7]. Gr〇〇tw用此方法考察了表面活性劑在聚合物表面 吸附的形式;Yuan等19’1?研究了表面活性劑與聚合物的相互作用.目前,將DPD方法應(yīng)用于淀粉乳液 體系的研究卻少有報(bào)道.
本文以環(huán)己烷為油相,淀粉乳液為水相,Span60和Tween60為乳化劑,用耗散粒子動(dòng)力學(xué)方法對(duì) 淀粉乳液體系的形成過程及油水比和乳化劑含最對(duì)淀粉乳液形成的影響進(jìn)行模擬,考察^乳液體系相 分離過程的微觀結(jié)構(gòu)變化及油水比和乳化劑含量的影響,并通過實(shí)驗(yàn)進(jìn)行驗(yàn)征.
1實(shí)驗(yàn)部分
1.1模擬方法
1.1.1粗粒化DPD模擬的基本思想是用1個(gè)“珠子”代替分子中的部分基團(tuán)或者流體中的團(tuán)狀物 質(zhì),作用在粒子上的力包括排斥力(”)、耗散力(〇和隨機(jī)力(K),每個(gè)珠子的運(yùn)動(dòng)符合牛頓運(yùn)動(dòng) 方程Ul — 13].根據(jù)分子在粗?;^程中每個(gè)珠子的摩爾體積大致相等的原則,本文的粗?;^程為:1 個(gè)環(huán)己烷分子為1個(gè)珠子,用〇表示[見圖1(A)]; Span60分子結(jié)構(gòu)如圖1(B),長(zhǎng)鏈由4個(gè)e3珠子表 示,其它用虛線隔開的每一部分作為1個(gè)珠子,用e,,e2表示;淀粉分子的1個(gè)單體作為1個(gè)珠子,用 s表示[見圖1(C)] ; Tween60結(jié)構(gòu)如圖1 (D)所示,聚氧乙烯鏈由幾個(gè)e4珠子表示,其它部分與 SPan60分子的劃分相同.模擬算出的各個(gè)珠子的摩爾體積為152 ~ 176 cmVmol,與文獻(xiàn)[M]給出的相 對(duì)應(yīng)單體結(jié)構(gòu)的實(shí)際摩爾體積(90 ~110cm3/m〇l)相比,雖不完全一致,但各珠子的大小變化趨勢(shì)與實(shí) 際相一致,因此本文采用的各個(gè)珠子的模擬體積是相對(duì)合理的•
實(shí)驗(yàn)方法
1.2.1實(shí)驗(yàn)材料可溶性淀粉、環(huán)己烷、乙酸乙酯、無水乙醇和氫氧化鈉(分析純,天津市大茂化學(xué) 試劑廣),環(huán)氧氯丙烷(分析純,上海凌峰化學(xué)試劑有限公司),Span60和Tween60(化學(xué)純,天津市科 密歐化學(xué)試劑有限公司),蒸餾水為自制.
1.2.2微球的制備將表面活性劑加入100 mL環(huán)己烷中,于45丈恒溫水浴加熱攪拌至完全溶解,把 油相倒入燒瓶并置于45 t恒溫水浴中待用.取一定量可溶性淀粉于錐形瓶中,加人去離子水調(diào)勻并 加人NaOH,于磁力攪拌下活化30 min.將水相逐滴加入到油相中,在液珠分散均勻后加人環(huán)氧氯內(nèi)烷 交聯(lián)3 h.反應(yīng)后離心,沉淀,分別用乙酸乙酯和無水乙醇洗滌,除雜后所得微球于60烘箱中干燥
至恒重,得白色至淡黃色粉末狀微球.
1.2.3結(jié)構(gòu)表征將淀粉、陰離子淀粉微球真空鍍金制樣后用XL-30型掃描電鏡(荷蘭飛利浦公司) 觀測(cè)形貌,并用Mastersize-2000型激光粒度分析儀(英國(guó)Malvern Inslrumenls, Ltd•公司)測(cè)量淀粉微球 的平均粒徑.
2結(jié)果與討論 2.1淀粉乳滴形成過程的模擬分析
圖2為隨模擬步數(shù)的增加體系內(nèi)各組分聚集形態(tài)的變化過程,其中環(huán)己烷、Span60、Tween60、淀 粉的體積比為0.5:0.037:0.0185:0.05,為清楚地觀察體系的演變過程,圖中未顯示環(huán)己烷分子-
模擬初期,Span60、Tween60與淀粉均無規(guī)則分散在環(huán)己烷中[圖2( A)].淀粉分子模擬100步時(shí) 開始聚集,隨著步數(shù)的增加,越來越多的淀粉聚集在一起,1〇〇〇步便已初步聚集成球形[圖2(B) ~ (E)].因?yàn)榈矸蹫樗苄跃酆衔?,在油介質(zhì)中有自發(fā)聚集的趨向,N時(shí)由于乳化劑分子降低丫油水界 面的張力使其逐漸向微球狀過渡;乳化劑分子則一部分發(fā)生自聚,一部分聚集在淀粉分子周圍,親水 珠子ei,e2, e4吸附在淀粉分子表面,親油碳鏈則伸向環(huán)己烷.模擬達(dá)到1〇〇〇步后,淀粉分子的微球狀基本不變,自聚的乳化劑分子則與淀粉分子作用,向淀粉微粒擴(kuò)散,吸附在其表面.模擬到6000步 時(shí),一個(gè)完整的淀粉乳滴開始形成,模擬發(fā)現(xiàn),即使經(jīng)過更K的模擬步數(shù),體系內(nèi)各組分的分布狀態(tài) 和相對(duì)位置幾乎不變,乳滴的構(gòu)型也不發(fā)生明顯變化,此時(shí)達(dá)到模擬平衡.但各組分的位置會(huì)有變化, 因此盒子的位置也隨0標(biāo)分子移動(dòng),使整個(gè)H標(biāo)分子始終顯示出來[圖2(G)和達(dá)到平衡時(shí),淀 粉聚集成球狀分介在環(huán)己烷中,乳化劑分子的親水基吸附在顆粒表面,而親汕基伸向油相,保持淀粉 微粒的穩(wěn)定.為了更有效地對(duì)模擬體系性質(zhì)進(jìn)行分析,本文屮所有的模擬都采用10000步這樣不僅 能判斷體系是否達(dá)到平衡,同時(shí)也能顯示、衡后體系的狀態(tài)- 2.2影響因素的模擬分析不同淀粉含量的模擬分析同定環(huán)己烷、Span60、, Tween6〇的體積比為0.5: 0.037:0.0185,分 別對(duì)不同淀粉含量(以環(huán)己烷為基準(zhǔn))的乳液體系進(jìn)行⑴〇〇〇少模擬,結(jié)果如圖3所示■當(dāng)?shù)矸酆钶^ 少時(shí)(環(huán)己烷和淀粉乳體積比為20:1),形成的乳滴表面乳化劑層緊密亂厚實(shí),并有過量的乳化劑分散 在體系屮,過分緊密的乳化劑層不利于交聯(lián)反應(yīng)的進(jìn)行,如圖3(A).隨著淀粉穴量增加(環(huán)己烷和淀 粉乳體積比為1〇:1),乳滴表層的乳化劑排列越來越疏松,如圖3(B).但當(dāng)?shù)矸酆吭黾拥揭欢繒r(shí) (環(huán)己烷和淀粉乳體積比為6. 67:1),體系屮的乳化劑反而不足,乳化不完全,如圖3(C)■繼續(xù)增加淀 粉含量(環(huán)己烷和淀粉乳體積比為3. 33:1),不能被乳化的淀粉越來越多,并發(fā)生聚集,形成淀粉分子 聚集體,巋淀粉達(dá)到-定量時(shí),形成了柱狀結(jié)構(gòu),如圖3(D).繼續(xù)增加淀粉的含量(環(huán)己烷和淀粉乳 體積比為2:1),體系變得更不穩(wěn)定,形成的結(jié)構(gòu)也更復(fù)雜,如圖3(E).
屮珠子之間的距離越來越小,相互碰撞粘連的機(jī)率增加,體系中出現(xiàn)柱狀結(jié)構(gòu)[圖4(D)].繼續(xù)減小 環(huán)己烷的量(環(huán)己烷和淀粉乳體積比為2:〗),體系會(huì)有從W/0向0/W過渡的傾向「圖4(E)].
2-2.4淀粉均方末端距變化情況聚合物鏈的末端距(/〇指聚合物鏈兩末端珠子之間直線距離的統(tǒng) 計(jì)平均值.均方末端距(/?:)指末端距平方的熱力學(xué)f•均,并僅與高分子鏈的首位2個(gè)鏈段的位昔冇 關(guān),實(shí)驗(yàn)原料為直鏈淀粉,止好適合用均方末端距(尺2)來表征淀粉分子的仲展性,即淀粉的聚集程 度,同時(shí)也在一定程度I•.反映廣微粒的粒徑大小h61.圖6反映了 h述淀粉分子的均方(KMS)末端矩變 化.由圖6可見,淀粉的均方末端矩隨淀粉用量的增加和環(huán)己烷用量的減少而增加,隨乳化劑用量的 增加先減少后增加.這足因?yàn)椋海?)隨著水相的增加,乳化劑分f相對(duì)減少,因此與淀粉分子之間的 相互作用也越來越小,使得淀粉分子伸展性增加;(2)汕相減少,親油基相對(duì)環(huán)己烷而言,密度增大, 從而使得乳化劑與環(huán)己烷相互作用增強(qiáng),淀粉乳粒伸展性增加;(3)隨著乳化劑分子數(shù)目的增加,原 聚集在淀粉骨架周圍的乳化劑分子開始?jí)嚎s聚合物,使淀粉的Z?1急劇下降,繼續(xù)增加乳化劑濃度,過 量的乳化劑分子與包圍微乳粒的乳化劑分子發(fā)牛相互作用,造成淀粉乳粒開始膨脹,上升.
工藝參數(shù)根據(jù)DPD模擬結(jié)果,由2. 2. 1節(jié)可得出汕水比范圍:〇. 5/0. 075 «7,0. 5/0. 025
2〇(模擬時(shí)以油相為基準(zhǔn));由2.2.2節(jié)可得出油水比范圍:0.35/0.05 =7, 1/0.05 =20(模擬時(shí)以水相 為基準(zhǔn));由2.2. 3節(jié)可得出乳化劑用量范圍:0.045/0.5 =9%, 0.09/0.5 = 18%.因此,形成穩(wěn)定淀 粉乳液體系的參數(shù)范圍為7 <油水比<20, 9% <乳化劑用量矣18%.
2.3淀粉微球?qū)嶒?yàn)
利用丨•.述模擬得出的乳液體系制備淀粉微球,研究不N油水比、不N乳化劑含量和不同乳化劑配 比對(duì)制備的影響.油水比分別為8: 1T 10: 1 [對(duì)應(yīng)圖3(B)的圖4(B)]和12: 1,14: 1,20: 1 [對(duì)應(yīng) 圖3(A)和圖4(A)];乳化劑含童分別為9% [對(duì)應(yīng)圖5(A)], 11%,12% [對(duì)應(yīng)圖5(B)], 13%, 15% [對(duì)應(yīng)圖5(D)], 18% [對(duì)應(yīng)圖5(1))].通過掃描電鏡觀察微球外貌、大小及分布情況.
油水比、乳化劑含量對(duì)淀粉微球形成的影響由圖8可知,固定其它因素不變,隨著油水比的 增大,微球的平均粒徑減小,這足因?yàn)槲⑶虻拇笮≈饕Q于乳液滴的大小,而乳滴的大小直接與水 相和乳化劑的摩爾比(/?值)有關(guān),在一定范圍內(nèi),#值越小,乳滴半徑越小…當(dāng)油水比增大時(shí),水相用 量相對(duì)減少,尺值也減小,因此微球粒徑減小•另外,隨油水比增大,微球的產(chǎn)率先增加后減少,并目. 油水比小于8時(shí)不能得到微球,油水比等于8時(shí),成球性不好,油水比在10?14時(shí)產(chǎn)率變化不大U成 球性好,油水比增大到20時(shí),產(chǎn)率很小.
同定其它因素不變,隨乳化劑用量增加,微球的平均粒徑先減小后增加,乳化劑含 量較低時(shí),不足以將兩相界面張力降低至穩(wěn)定的乳狀液,油相中的小乳滴聚集在-•起形成較大 的乳滴,導(dǎo)致粒徑偏大,隨著乳化劑含量增加,穩(wěn)定的乳滴逐漸形成,《值相應(yīng)減小,從而導(dǎo)致粒徑減 小,但當(dāng)乳化劑用置增加到一定程度時(shí),乳滴表層表面活劑相對(duì)過雖,乳滴之間發(fā)生粘連,導(dǎo)致微球 粒徑增大.另外,隨乳化劑用量的增加,微球產(chǎn)率減少,并且乳化劑用量過多,微球表面的過量乳化劑 難以洗除,使后處埋消耗大.
3結(jié) 論
用耗散粒子動(dòng)力學(xué)方法研究了淀粉乳液的形成過程及水油比、乳化劑含量?jī)梢蛩氐挠绊?模擬結(jié) 果表明,當(dāng)乳液體系到達(dá)穩(wěn)定平衡狀態(tài)時(shí),淀粉聚集成球狀分布在環(huán)己烷中,乳化劑分子的親水基吸 附在顆粒表面,而親油基伸向油相,保持淀粉微粒的穩(wěn)定.模擬分析結(jié)果表明,淀粉乳液體系中乳滴 粒徑的變化趨勢(shì)與2種乳化劑的配比無明顯關(guān)系,但隨淀粉含量的增加而增加,隨環(huán)己烷含量的減小 而增加,隨乳化劑含量的增加先減小后增加.形成穩(wěn)定淀粉乳液體系的參數(shù)范圍為7 <油水比矣20, 9%<乳化劑用量專18%.實(shí)驗(yàn)1j模擬結(jié)果吻合.DPD方法可以直觀地描述淀粉乳液的形態(tài),較好地描 述乳液體系的微觀結(jié)構(gòu),這有助于/解復(fù)雜乳液體系的微觀結(jié)構(gòu),并能對(duì)實(shí)驗(yàn)現(xiàn)象進(jìn)行分析,可為淀 粉微球的制備提供指導(dǎo).